FDM 3D Printing
From mechanical performance to versatility, discover the right balance with FDM materials for 3D printing.
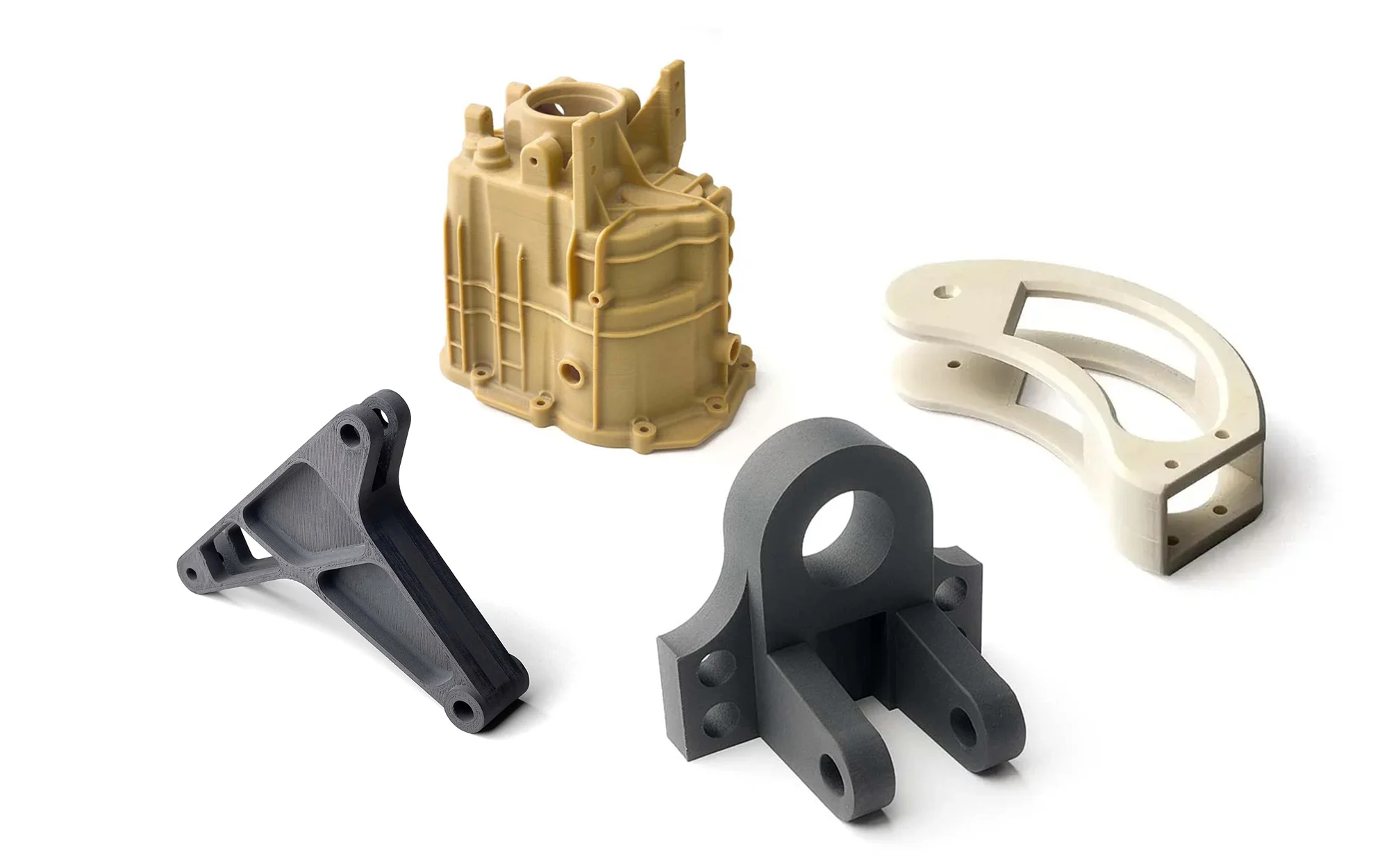
Materials and filaments used in FDM 3D printing
QUOTE IN 1 SECOND
turn your ideas into reality
Upload your 3D file to get closer to the production of your parts.
free instant quoteWhat is FDM 3D printing
FDM, which stands for Fused Deposition Modelling, is a process in which a filament of thermoplastic material, often called 'filament', is fed through a heated nozzle. The molten material is deposited layer by layer onto a build surface, following the path programmed by the three-dimensional (3D) digital file. As the individual layers cool and solidify, successive layers are created until the desired object is obtained. This 3D technology is widely used due to its versatility and accessibility, making it an optimal choice for enthusiasts and industries alike.
The FDM printer represents a milestone in custom prototyping and manufacturing due to its ability to process a wide range of thermoplastic polymers. This printing technology offers the opportunity to work with polymers with high mechanical, thermal and chemical performance, enabling the creation of robust components suitable for specific challenges in different industries. However, an inherent challenge of FDM printing is the support structures required to ensure stability during the construction of complex geometries. This limitation requires careful design and an additional stage of media removal, but despite this, the versatility offered by FDM printing continues to make it a crucial choice for the production of prototypes and customised components.
FDM Materials
The versatility of FDM 3D printing is evident in the wide range of materials it can use. Among the most common materials are Peek, ABS (acrylonitrile butadiene styrene) and polycarbonate. Each has its own unique properties, such as strength, flexibility and melting temperature, which make it suitable for different applications.
Nylon PA12 Carbon Fiber
Nylon PA12 CF is characterised by exceptional mechanical and thermal properties. This material is ideal for applications requiring strength, durability and the ability to cope with temperature variations. Its high mechanical and thermal properties make it essential in industries such as aerospace and automotive.
Peek
PEEK is a high-performance thermoplastic material, outstanding in mechanical strength, thermal stability and chemical resistance. Although cost and processing can be a challenge, its strength makes it ideal for applications requiring high performance.
Peek Carbon Fiber
PEEK CF, filled with carbon fibre, takes PEEK to new levels of performance. This material combines the exceptional characteristics of PEEK with the added lightness and rigidity of carbon fibre. Its exceptional mechanical performance makes it suitable for Metal Replacement practices under extreme conditions.
Peek Glass Filled
Glass-fibre filled PEEK GF offers high strength and stiffness, along with outstanding chemical and thermal resistance. Widely used in the electrical, aerospace and automotive industries, this lightweight and durable material can withstand high temperatures and prolonged use.
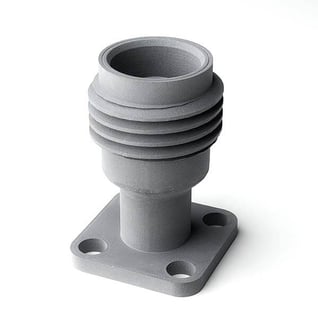
ASA
ASA (Acrylonitrile Styrene Acrylate) has established itself as a versatile material for 3D printing, with a significant advantage in UV resistance, ideal for outdoor applications. Its superior mechanical strength makes it a reliable choice for automotive and aerospace components under mechanical stress. However, the print finish may require additional processing, and the limited chemical and thermal resistance may require application-specific evaluations.
ABS medical
Medical ABS is a material certified as a USP 88 Class VI medical device, ensuring maximum compatibility and safety in medical environments. This ABS offers good temperature resistance, ductility and sterilisation possibilities, making it essential for the creation of prostheses, medical instruments and healthcare equipment.
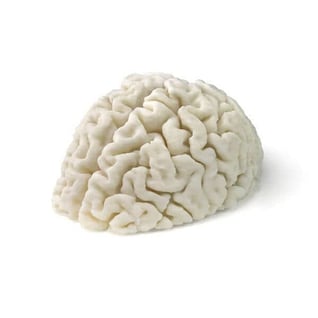
ABS Food
Certified for food contact, Food Grade ABS is a reliable choice in 3D printing for components intended for use with food. It offers a balanced combination of mechanical properties, including ductility and temperature resistance, ensuring food safety, dishwasher-safe and adaptability to a variety of food applications.
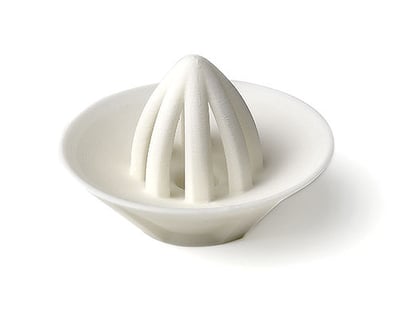
Polycarbonate
Polycarbonate offers an unrivalled combination of strength, layer adhesion and mechanical properties. However, the need for removable substrates and the fingerprint-sensitive black finish can present challenges.
ECOtech
ECOtech represents a breakthrough in 3D printing, offering high performance with flexural strength, limited deformation and a high-quality surface finish. FDA-approved for food contact and biodegradable to DIN EN ISO 14855 standards, ECOtech also stands out for its sustainability, making it ideal for high-performance and environmentally responsible applications.
PPS GF
Glass-fibre filled PPS GF offers outstanding mechanical strength due to the glass fibres, with improved dimensional stability and wear resistance. With superior thermal properties for high-temperature situations, PPS GF may exhibit reduced impact resistance and anisotropy, aspects to be carefully considered.
Nylon PA6 CF
Nylon PA6 CF is a composite material that combines carbon fibre with nylon, offering superior chemical resistance, low friction and exceptional impact strength. However, the presence of carbon fibre can complicate colouring and make layers more visible in 3D printing. Despite these challenges, Nylon PA6 CF is an excellent choice for industries requiring light weight, strength and dimensional stability.
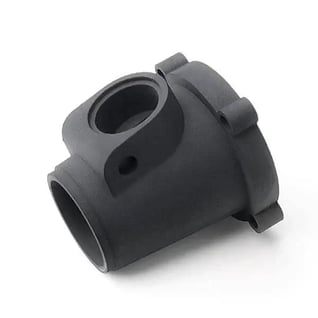
Online FDM 3D printing service at Weerg
Weerg, one of the main online services for FDM 3D printing, has a number of key advantages that make it a reliable and comprehensive choice for 3D production.
The 3D file of the desired model is processed by slicing software, which breaks it down into layers of the desired thickness and generates a G-code file. This file describes to the printer the axis movements required to create the part. The FDM printer then melts the solid plastic filament and extrudes it layer by layer through a nozzle, thus forming the 3D object on the build surface.
Among the key advantages of FDM are its priority mechanical properties. This printing technology offers metal replacement materials and performance, making it ideal when robustness and strength are paramount. Thanks to the wide range of materials offered by Weerg, users can select the most suitable solution for specific project requirements, ensuring maximum customisation and flexibility.
The intuitive interface of Weerg's online service simplifies the ordering process, allowing users to easily upload their CAD files, customise print options and obtain instant quotes. This user-friendly approach is crucial for efficient and rapid management of 3D printing projects.
Weerg also stands out for fast delivery, thanks to optimised production processes and timely shipping. This is a key element for those looking for 3D solutions with tight lead times, without compromising the quality of the final product.
Dedicated customer service completes the user experience, offering active support and ready to answer user questions, providing assistance throughout the production process. This commitment to customer satisfaction contributes to a positive and smooth relationship.
Finally, cost transparency is another element that characterises Weerg. Users receive clear and detailed quotations before confirming their order, avoiding unwelcome surprises and ensuring competitive value for money.
Instant quote for your FDM parts
Upload your 3D file and realise your designs now
free instant quote